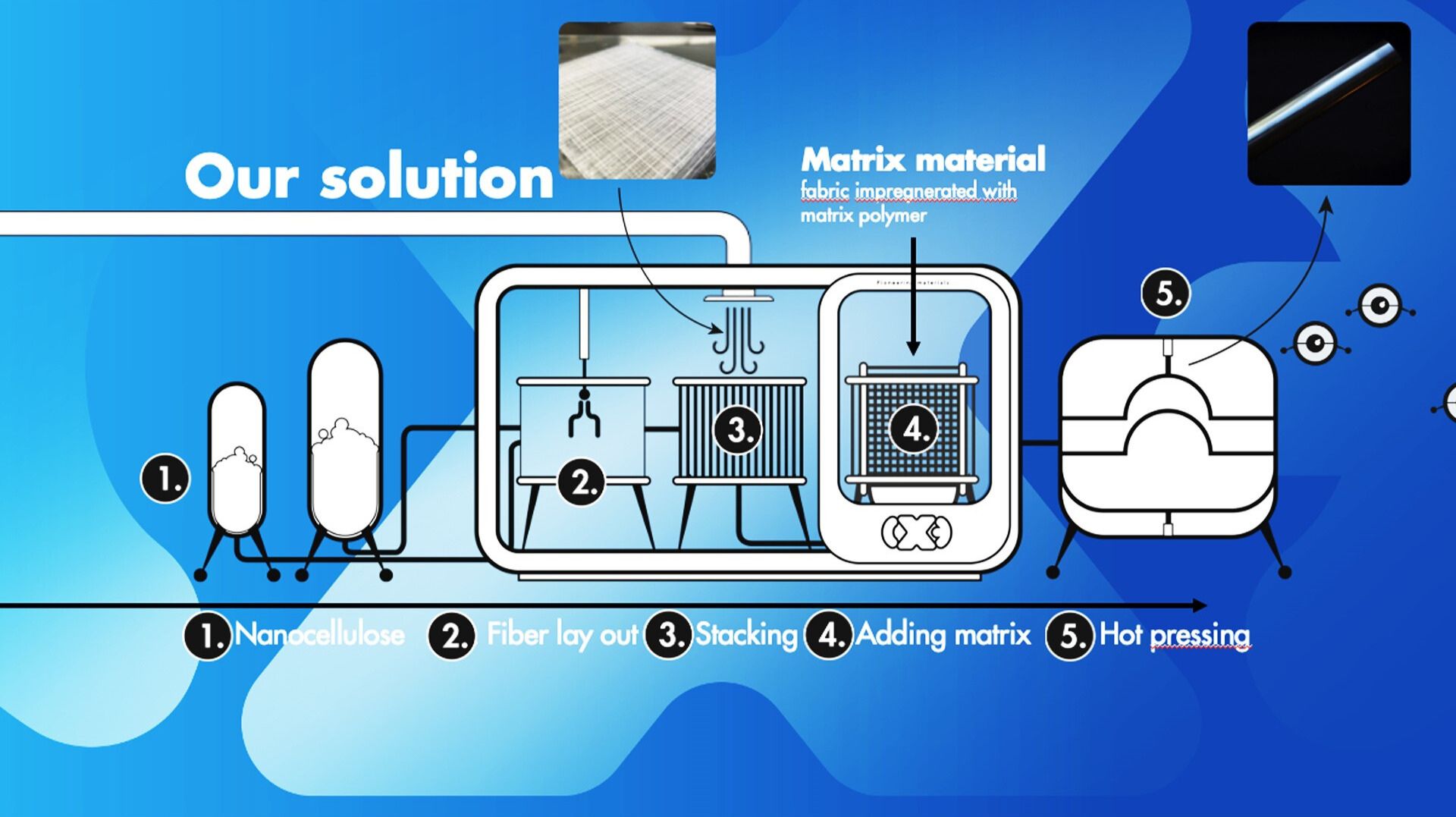
Iinnovation
Background
Lightweight materials have played and will continue to play a crucial role in the transition towards a sustainable society. They enable energy-efficient transportation (vehicles, trains, and aircraft) and the production of renewable energy (wind and wave power). The significant contribution arises from combining high performance/functionality with high material efficiency and thus lower weight, reducing energy consumption in transportation, for example.
Despite the essential contributions of composite materials to the transition and their high efficiency during the use phase, the composite industry faces sustainability challenges. These challenges emanate from demanding and fossil-intensive manufacturing processes and issues with recycling and end-of-life management. Another challenge is material utilisation in the manufacturing chain. Production waste is estimated at 30-50% for carbon fibre composites. Another concrete example is decommissioned rotor blades from wind turbines, which are currently accumulating with almost no recycling possibilities for fibre-reinforced composites (carbon and glass fibre), with the most common solution being landfills.
In light of this, CelluXtremes has developed a unique technology platform with the potential to increase the use of lightweight materials. The patented technology enables spinning strong fibres from 100% nanocellulose (from standard pulp) using a water-based process based on green chemistry and low emissions. Additionally, the spun fibres can be formed into custom reinforcement structures in a single step, without waste, which can then be impregnated with a polymer matrix to form a strong, rigid composite material. The technology originates from research conducted at KTH within the Wallenberg Wood Science Centre. It has been further developed in terms of capacity and scalability over the past year, including through a proof-of-concept project at KTH funded by the Knut and Alice Wallenberg Foundation.
CelluXtreme owns the basic spinning technology patent, and most inventors are involved in the company. Another patent application has been submitted where the technology has been further developed into a method to directly form reinforcement structures (without the need to spin a continuous fibre that needs surface treatment and weaving to finally be cut into the desired shape), with the potential to place each fibre where it is most beneficial. These results have nowbeen implemented in a pre-pilot process for producing structured fabrics.
CelluXtremes’ production technology will be able to deliver biobased, advanced, and sustainable composite materials based on energy- and material-efficient production in compact manufacturing units with high degrees of automation and customisation, where the composite materials produced have unique material properties.
CelluXtremes’ future customers are companies manufacturing components or products from advanced composite materials. CelluXtreme has been and is in contact with a large number of companies. Gradually, the dialogue has focused on segments and customers where CelluXtremes’ potential to offer a unique solution is significant. Specifically, this means advanced sustainable composite materials possessing unique properties and functionality that customers demand. Examples include composites for aerospace applications, drones, electric motor drives, and battery enclosures. In these application areas, the ability to pay is considered high and offers good margins over time.
Why is this important?
Increased energy and resource efficiency are prerequisites for creating ecological, economic, and social sustainability. The need for increased resource utilisation is accelerated by pandemics and conflicts that slow down globalisation. This, in turn, sharpens the demands for self-sufficiency due to shortages of materials, energy, and secure supply chains. National and European strategies and directives aim to drive the development of sustainable materials, products, and value chains. This will strongly impact how we manufacture, use, and circulate materials. In this perspective, lightweight innovation is an enabler whose potential needs to be fully explored.
Today, we use advanced fibre composites in many different applications, and lightweight technology has played a crucial role in achieving resource- and energy-efficient constructions and products and will continue to do so. Lightweight technologies significantly enable the world to meet critical societal challenges based on the UN’s 17 global sustainability goals in Agenda 2030. However, there are clear challenges related to energy consumption, the use of challenging chemicals, and significant waste in manufacturing. Recycling of lightweight materials such as glass fibre and carbon fibre composites is currently minimal. The polymer matrix can usually be dissolved, but the fibres are difficult to recycle. Most composite materials, therefore, end up in landfills today.
For CelluXtremes’ material concept, there are sustainability benefits in all stages: the starting material, the process, the use, and the recycling. The starting material is cellulose fibres, which can be extracted from most plants on Earth, which in turn can contribute to reduced transportation needs. Sustainable forest raw materials offer a large-scale source of cellulose fibres with known properties, and the cellulose fibres can be refined into nanocellulose.
From a supply perspective, it can be stated that today’s advanced composite material solutions are heavily dependent on a complex global value chain. Materials are manufactured with fossil raw materials, with high emissions, extensive use of chemicals in production, and low recycling rates. Entirely new concepts must be introduced for future lightweight materials. CelluXtreme will contribute by replacing today’s advanced composite materials with a compact value chain that utilises local raw materials and principles of additive manufacturing, which will have broad societal effects. This will reduce the need for manufacturing in, for example, Asia.
From a resource utilisation perspective, the manufacturing process, where nanocellulose is directly spun into custom fibre structures, reduces manufacturing waste. CelluXtremes’ composite material also has the potential to recycle the ”building blocks” of the fibres, which can then be used to produce new fibres. Additionally, biobased fibres can always be recycledas bioenergy with zero net carbon dioxide emissions.
Technology
CelluXtreme’s overarching goal is to develop a production line that can deliver biobased, advanced, and sustainable composite materials based on energy- and material-efficient production in compact manufacturing units with a high degree of automation and customisation and where the composite materials produced have unique material properties.
The heart of this production will be manufacturing units based on CelluXtremes’ patented technology to spin strong fibres from 100% nanocellulose. These units will deliver two- and three-dimensional fibre structures without the need for intermediate steps such as manufacturing fibre rolls or fabrics manually trimmed to the desired geometry, as required in today’s composite material value chain. Additionally, each fibre structure produced should be able to be unique without affecting productivity.
Customer Value
The overarching challenges are met by CelluXtremes’ new and unique technology for manufacturing biobased composite materials with high performance and complexity that can compete with today’s high-performance composites and offer a solution to mitigate the problems they face with recycling and end-of-life. CelluXtremes’ value creation can be summarised as follows:
- Manufacturing of advanced and functionalised composite materials according to customer needs. Production is based on additive manufacturing, which enables the manufacture of customised reinforcement structures without costly manual labour in an automated process, reducing variation in the properties of manufactured details. This is impossible in the value chain for any competing concepts for reinforcement fibres, even though there are concepts for robotic fibre placement under development.
- A compact value chain that can be established locally and scaled gradually. Value creation can occur locally and will contribute to creating competitiveness and employment in Sweden. In the case of conventional composites, a significant portion of value creation occurs outside of Europe.
- A material concept designed for recycling with retained properties or net-zero carbon dioxide emissions. Traditional composites cannot be easily recycled. The polymer matrix can usually be dissolved, but the fibres are difficult to recycle. Most fibre materials, therefore, end up in landfills today. CelluXtremes’ composite material has the potential to recycle the ”building blocks” of fibres, which can then be used to produce new fibres. In the worst case, incineration of CelluXtremes’ products is simple and produces heat with a net-zero emission, i.e., as bioenergy.
- The simplified value chain makes it easy for the customer to assess their environmental impact since there are only a few input flows, and the chemistry follows the principles of green chemistry. None of these is available for conventional reinforcement fibres, which have a significant number of supplier steps and use a wide range of advanced chemicals.
- The surface properties of CelluXtremes’ fibres eliminate the need for chemicals for surface treatment, and the active surfaces enable the addition of other components to the composites, enabling additional functionality (beyond strength and stiffness).